Il monitoraggio delle condizioni migliora l’affidabilità dei sistemi di alimentazione elettrica
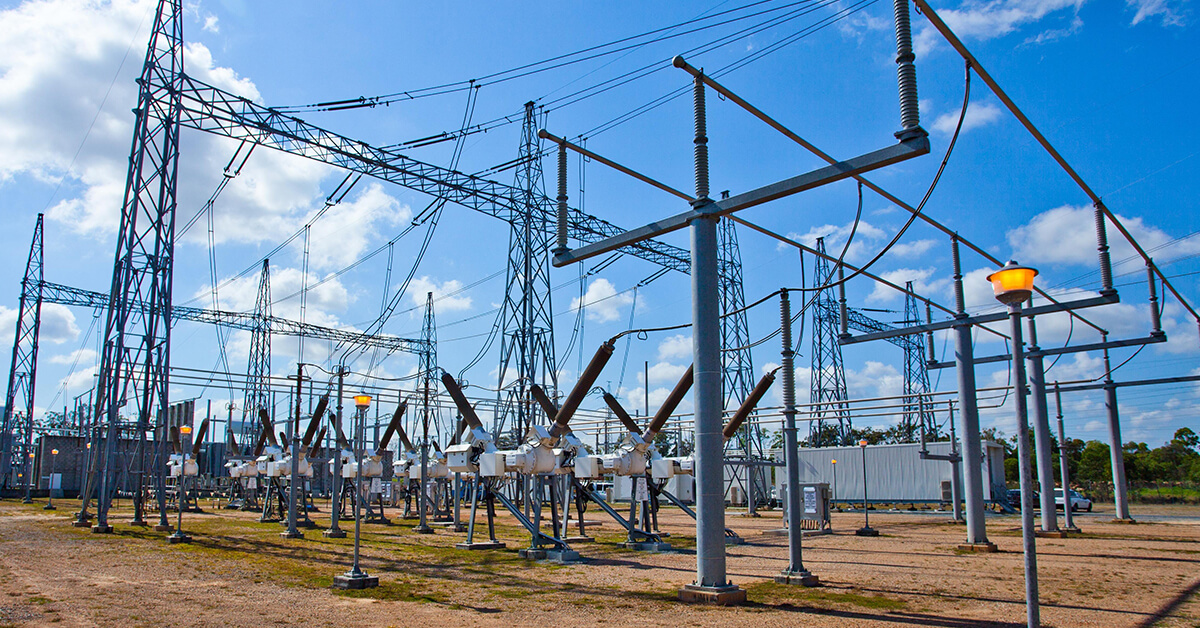
I fornitori di energia elettrica devono gestire un’infrastruttura obsoleta che aumenta il rischio di cadute di tensione, con conseguenti cali di tensione o guasti di sistema che comportano dei blackout. La manutenzione non pianificata di questi sistemi è costosa e molte aziende sono alla ricerca di nuovi modi per rilevare eventuali guasti imminenti prima che si verifichino. Grazie al monitoraggio continuo delle condizioni, i fornitori di energia elettrica possono individuare i problemi in anticipo e pianificare la manutenzione in modo appropriato, migliorando l’affidabilità del sistema e riducendo i costi.
L’utilizzo di una termocamera fissa per monitorare le apparecchiature critiche nelle sottostazioni e nell’intera rete elettrica può aiutare gli addetti alla manutenzione a risolvere i problemi in modo tempestivo quando è più facile gestirli. Ad esempio, le perdite di fluido o i difetti di isolamento all’interno di un trasformatore causano surriscaldamenti che possono provocare un effetto domino di guasti, ma molti fornitori di energia elettrica non dispongono di sistemi automatici di rilevamento termico in grado di segnalare questi problemi. Il risultato può essere un’enorme interruzione di corrente con effetti su attività commerciali, produzione, lavori pubblici e sistemi di controllo del traffico. Naturalmente, il fornitore di energia elettrica colpito può subire gravi perdite finanziarie e può dover sostenere costi enormi per rimettere in funzione i propri sistemi.
Prima di guastarsi, le apparecchiature ad alta tensione tendono a riscaldarsi; il monitoraggio continuo delle loro condizioni con una termocamera fissa può aiutare i fornitori di energia elettrica a individuare eventuali guasti imminenti prima che si verifichino.
I componenti di una sottostazione che si riscaldano quando si prepara un malfunzionamento comprendono:
- Trasformatori di potenza (livello dell’olio e funzionamento della pompa)
- Commutatori di carico (livelli dell’olio, altri problemi interni)
- Scaricatori di fulmini (degradazione dei dischi in ossido di metallo)
- Sezionatori (perdite di olio o SF6)
- Interruzioni meccaniche (connessioni difettose, contaminazione)
- Armadi di comando (usura di ventilatori, pompe e altri componenti)
Il rilevamento di aumenti di temperatura in questi componenti mediante l’uso di termocamere consente di avviare operazioni di manutenzione preventiva prima che si verifichi un'interruzione non pianificata a causa di un guasto effettivo.
Anche se la maggior parte dei fornitori di energia elettrica impiega già termocamere portatili per controllare regolarmente le apparecchiature delle sottostazioni, molti stanno ora installando sistemi di termocamere fisse per garantire il monitoraggio 24 ore su 24, 7 giorni su 7. Le videocamere intelligenti progettate con edge computing per allarmi e analisi, come la videocamera con sensore avanzata FLIR A70 Smart Sensor, offrono una soluzione semplificata.
Questi sistemi utilizzano tecnologie di rilevamento e misurazione, metodi di controllo e comunicazioni digitali avanzati. Possono prevedere, rilevare e segnalare rapidamente agli addetti alla manutenzione eventuali problemi imminenti, riducendo così la possibilità di guasti del sistema, blackout e perdita di produttività.
Ad esempio: in un impianto europeo di grandi dimensioni è stato scoperto un isolatore surriscaldato in una sottostazione di trasformazione che è stato riparato a un corso di circa 1.400 $. Prima dell’implementazione del programma di rilevazione termografica, in passato un problema simile avrebbe causato un guasto con conseguenze catastrofiche ed un costo di oltre 2,7 milioni di dollari.
Fai clic per saperne di più sulle videocamere fisse FLIR A50/A70 Smart Sensor, oppure contatta un esperto di FLIR per ulteriori informazioni.